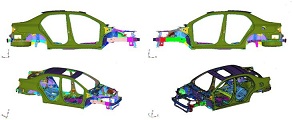
在現代汽車設計過程中,車身結構強度的好壞直接影響到整車的疲勞壽命、碰撞、振動等諸方面性能,因此,對車身進行強度分析可以及時驗證設計方案的合理性,改進設計方案,縮短開發(fā)周期,提高設計效率,降低設計成本,具有重要的現實意義。車身強度有限元分析時,載荷邊界條件非常復雜,既有來自地面和貨物的外界激勵,也有來自發(fā)動機的內部激勵。為了簡化分析,忽略了發(fā)動機的內部激勵,只考慮發(fā)動機質量、貨物質量和地面的外界激勵。通過對客車實際工作狀態(tài)的分析,共模擬了汽車在滿載、制動、轉彎、右前輪抬起150mm、左后輪抬起150mm、右前輪和左后輪同時抬起15°六種工況下整車受力狀況,找出高應力區(qū),考察其零部件的強度是否滿足要求,并提出相應建議。
客車車身涉及上百個零部件,數量之多、結構復雜,導致網格劃分工作量巨大。對于左右對稱的零件,只需取一側模型,另一側網格則可通過鏡像來實現,這樣既提高了網格劃分的效率又保證了結構的對稱性。對于小的線路支架、焊接螺母安裝支架等不影響整車性能的小部件可以不進行網格劃分,但車架上的發(fā)動機安裝支架和起加強作用的小支架必須進行網格劃分。對于零件中帶有的一些小孔、翻邊、小的加強筋、細小的幾何過度等特征,為了提高網格質量,需要對這些零件進行一定的簡化。
根據設計部門提供的白車身三維模型建立起來的有限元模型如圖所示?蛙囓嚿硭辛悴考捎冒鍤卧猄HELL進行劃分,盡量采用四邊形單元模擬,少量三角形單元過渡以滿足高質量網格需求。白車身有限元模型總計網格325951個,其中四邊形單元311610個,三角形單元14341個,三角形單元所占的比例為4.40。車身結構中的零件連接方式主要是焊接,其次是螺栓連接。而焊接又以點焊為主,小部分采用邊焊江氧化碳保護焊。不同的連接形式采用不同的處理方法,點焊的簡化方法是在焊點位置處采用CWELD單元,車架上管梁和縱梁的連接采用節(jié)點藕合。螺栓連接采用RBE2單元模擬,粘膠采用六面體單元模擬。強度分析模型按整車滿載質量1980kg計算,白車身的附加質量用質量點單元CONM2模擬,發(fā)動機、變速箱、油箱、備胎、水箱、冷凝器、前門總成、中門總成、后背面總成、發(fā)動機罩總成和座椅及乘員質量使用RBE2剛性單元加載到相應總成的安裝處。內飾件和其它未包含于表中的質量按質量點的形式加載到前、后縱梁及對應地板上。該款微型客車的乘員人數為5~8名,為了滿足車身在不同情況下的承載要求,以8名乘員駕駛室2名,乘員艙6名計算車身所受的乘員載荷。
專業(yè)從事機械產品設計│有限元分析│強度分析│結構優(yōu)化│技術服務與解決方案
杭州那泰科技有限公司
本文出自杭州那泰科技有限公司www.hanpinfa.cn,轉載請注明出處和相關鏈接!