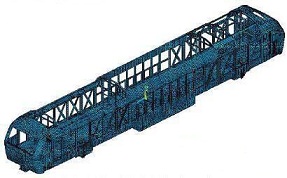
目前,國內外關于提高客車速度的方法有兩點:一是提高輪軌間的豁著力,二是降低車體自重。但要提高客車車輪與輪軌間的豁著力,必須要提高客車的牽引動力或改變車輪與鋼軌的材料來增大它們之間的摩擦力?墒沁@兩種提高輪軌間粘著力的方法與降低車體自重相比就顯得很麻煩。所以,通過有限元分析改變車體的自重來提高客車速度是個既經濟又容易實施的措施。
通過以下兩種措施可降低車體自重。
(1)選擇合適的材料世界各國高速列車用材情況已從普通鋼、耐候鋼發(fā)展到不銹鋼、鋁合金及纖維復合增強塑料,但目前國內外高速列車車體主要用材傾向于鋁合金,主要是由于鋁型材具有減重效果好、耐腐蝕,維修費低、制造工藝簡單、節(jié)省加工費用以及良好的運行品質等優(yōu)點。
(2)優(yōu)化車體結構車體結構從最開始的骨架外殼結構發(fā)展到雙殼結構,這種結構具有兩方面的優(yōu)熱:①能夠達到高剛性、增加噪音透過損失,提高車內的乘車舒適度;②大幅減少零件數(shù)量,擴大自動化焊接范圍,從而降低制造成本,提高質量。
為提高客車速度,要盡可能降低車輛的自重,所以采用全鋁合金結構,并廣泛采用大型中空截面擠壓型材,在保證車體具有足夠強度和剛度的前提下,使材料得到最充分的利用。使用鋁合金作為車體材料的最大優(yōu)點是輕量化。其目的是減少運行成本和維護成本,特別是用于高速車輛時,有助于達到高速化。隨著近年來的鋁合金擠壓型材的大型化和輕薄化,車體結構可由大型輕薄的擠壓型材組合構成,縱向可以大幅度采用自動焊接,提高了質量和生產率,所以高速客車車體越來越多地采用鋁合金材料。
鋁合金車體的橫斷面結構采用筒形結構。車體的底架、側墻以及車頂采用大型空心截面的擠壓鋁型材拼焊而成。底架地板由上下翼板、斜筋板和腹板組成,采用中空擠壓型材,長度可達車體全長。下側梁、側墻板、車頂板亦采用形狀各異的中空截面擠壓鋁型材。
車體結構設計主要有以下四部分:
(1)底架底架位于車體下部,是車體的基礎,也是主要的承載構架。車體兩側為側墻結構,車體前端為前端墻,后端是車體后端墻,它們都焊裝在底架上。底架上面還焊有設備安裝骨架,它是車內各種設備安裝的基礎。車身底架包括牽引梁、枕梁、側梁(邊梁)、端梁和波紋地板等。底架全長25500mm,寬3140mm。在距兩端3750mm處是枕梁的中心線,枕梁對稱布置。
(2)側墻結構高速客車車體側墻采用大型中空擠壓鋁型材,不設車內側立柱,型材之間的焊接為在車體長度方向上連續(xù)焊接的方式,側墻與車頂?shù)穆?lián)結采用車內側、車位側連續(xù)焊接,側墻和底架邊梁之間的聯(lián)結采用車內側點固焊接,車外側連續(xù)氣密焊接。
側門中間部分主要由側板和腰板組成,窗口及其以下部分稱側板,通長板有4塊,其中窗口部分由窗上、窗下通長板預先銑口與窗間板拼焊而成,兩端通到門區(qū)部分,腰板由3塊通長板組成,均通到外端與端墻搭接,通長板均為中空型材結構。窗口部分根據(jù)窗的安裝結構關系焊接。
門區(qū)部分即側門出入口部分,根據(jù)門口與外端距離的大小分成板梁式結構和板梁加型材結構兩種形式。
側墻結構(簡稱側構)主要由側地板和車頂側梁及各種縱、橫梁組焊構成,是車體承載結構的重要組成部件。側構總長25500mm,側面高2100mm,側墻的一側開有兩扇門,其尺寸是1100mmx1900mm,在離前端墻850mm處開有2000mmx700mm的八扇窗。每扇窗子之間的距離為400mm。
(3)車頂結構車頂由7塊縱向與車體等長的中空型材板插接對焊而成,不設車頂彎梁與縱梁,在內部設有筋板。車頂由半徑分別為6000mm和兩個500mm的三段圓弧過渡而成。車頂?shù)膬韧獍逡约靶卑搴穸染?.5mm,全部采用7050-T7651型材擠壓而成,車頂斷面。
中間車的車頂焊接件有空調座、空調排水管、通風管座、通風管、接地連接塊、設備支架、空調進風口、空調出風口等部件。
(4)端墻結構端墻根據(jù)車輛衛(wèi)生間和洗臉間的布置主要分為兩種結構:分體式和整體式。在端部設有衛(wèi)生間和洗臉間的車輛,其端墻為分體結構,另一端為整體式。
專業(yè)從事機械產品設計│有限元分析│強度分析│結構優(yōu)化│技術服務與解決方案
杭州那泰科技有限公司
本文出自杭州那泰科技有限公司www.hanpinfa.cn,轉載請注明出處和相關鏈接!